
Stainless steel is a group of iron-based alloys that contain a minimum of approximately 11% chromium, a composition that prevents the iron from rusting and also provides heat-resistant properties. Different types of stainless steel include the elements carbon, nitrogen, aluminium, silicon, sulfur, titanium, nickel, copper, selenium, niobium, and molybdenum. Specific types of stainless steel are often designated by a three-digit number, e.g., 304 stainless.

Argon oxygen decarburization (AOD) is a process primarily used in stainless steel making and other high grade alloys with oxidizable elements such as chromium and aluminum. After initial melting the metal is then transferred to an AOD vessel where it will be subjected to three steps of refining; decarburization, reduction, and desulfurization. AOD was invented in 1954 by the Lindé Division of The Union Carbide Corporation.

Austenitic stainless steel is one of the five classes of stainless steel by crystalline structure. Its primary crystalline structure is austenite and it prevents steels from being hardenable by heat treatment and makes them essentially non-magnetic. This structure is achieved by adding enough austenite stabilizing elements nickel, manganese and nitrogen.

Harry Brearley was an English metallurgist, credited with the invention of "rustless steel". Based in Sheffield, his invention brought affordable cutlery to the masses, and saw an expansion of the city’s traditional cutlery trade.
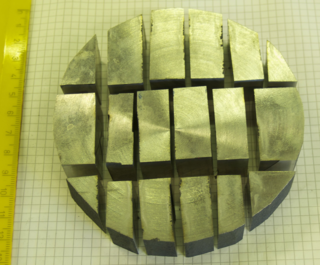
Duplex stainless steels are a family of stainless steels. These are called duplex grades because their metallurgical structure consists of two phases, austenite and ferrite in roughly equal proportions. They are designed to provide better corrosion resistance, particularly chloride stress corrosion and chloride pitting corrosion, and higher strength than standard austenitic stainless steels such as Type 304 or 316. The main differences in composition, when compared with an austenitic stainless steel is that the duplex steels have a higher chromium content, 20–28%; higher molybdenum, up to 5%; lower nickel, up to 9% and 0.05–0.50% nitrogen. Both the low nickel content and the high strength give significant cost benefits. They are therefore used extensively in the offshore oil and gas industry for pipework systems, manifolds, risers, etc and in the petrochemical industry in the form of pipelines and pressure vessels. In addition to the improved corrosion resistance compared with the 300 series stainless steels duplex steels also have higher strength. For example, a Type 304 stainless steel has a 0.2% proof strength in the region of 280 N/mm2, a 22%Cr duplex stainless steel a minimum 0.2% proof strength of some 450 N/mm2 and a superduplex grade a minimum of 550 N/mm2.

Marine grade stainless alloys typically contain molybdenum to resist the corrosive effects of NaCl or salt in seawater. Concentrations of salt in seawater can vary, and splash zones can cause concentrations to increase dramatically from the spray and evaporation. SAE 316 stainless steel is a molybdenum-alloyed steel and is the second most common austenitic stainless steel. It is the preferred steel for use in marine environments because of its greater resistance to pitting corrosion than other grades of steel without molybdenum. The fact that it is negligibly responsive to magnetic fields means that it can be used in applications where a non-magnetic metal is required. A fully austenitic grade, even when cold worked, is Nitronic 50. An example of a non-molybdenum grade performing well in seawater is Nitronic 60. "The pitting resistance of NITRONIC 60 in sea water is actually better than Type 316 due to the high levels of Si and N. The N also increases the yield strength . . ."

Stainless steels may be classified by their crystalline structure into four main types: austenitic, ferritic, martensitic, and duplex. Martensitic stainless steel is a specific type of stainless steel alloy that can be hardened and tempered through multiple ways of aging/heat treatment.

Panel edge staining is a naturally occurring problem that occurs to anodized aluminium and stainless steel panelling and façades. It is semi-permanent staining that dulls the panel or façade's surface, reducing the natural lustre and shine produced by the anodizing processes used on the aluminium. Panel edge staining may also appear on powder coated aluminium, painted aluminium, stainless steel and titanium surfaces.

SAE 304 stainless steel is the most common stainless steel. The steel contains both chromium and nickel [1] metals as the main non-iron constituents. It is an austenitic stainless steel. It is less electrically and thermally conductive than carbon steel and is essentially-magnetic but less magnetic than steel. It has a higher corrosion resistance than regular steel and is widely used because of the ease in which it is formed into various shapes.

SAE 316L grade stainless steel, sometimes referred to as A4 stainless steel or marine grade stainless steel, is the second most common austenitic stainless steel after 304/A2 stainless steel. Its primary alloying constituents after iron, are chromium, nickel (10–12%) and molybdenum (2–3%), with small (<1%) quantities of silicon, phosphorus & sulfur also present. The addition of molybdenum provides greater corrosion resistance than 304, with respect to localized corrosive attack by chlorides and to general corrosion by reducing acids, such as sulfuric acid. 316L grade is the low carbon version of 316 stainless steel. When cold worked, 316 can produce high yield and tensile strengths similar to Duplex stainless grades.

VG-10 is a cutlery grade stainless steel produced in Japan. The name stands for V Gold 10, or sometimes V-Kin-10 (V金10号). It is a stainless steel with a high carbon content containing 1% Carbon, 15% Chromium, 1% Molybdenum, 0.2% Vanadium, and 1.5% Cobalt.