An aircraft engine, often referred to as an aero engine, is the power component of an aircraft propulsion system. Most aircraft engines are either piston engines or gas turbines, although a few have been rocket powered and in recent years many small UAVs have used electric motors.
This is an alphabetical list of aircraft engines by manufacturer.

The aircraft diesel engine or aero diesel is a diesel-powered aircraft engine. They were used in airships and tried in aircraft in the late 1920s and 1930s, but never widely adopted beyond this. Their main advantages are their excellent specific fuel consumption, the reduced flammability and somewhat higher density of their fuel, but these have been outweighed by a combination of inherent disadvantages compared to gasoline-fueled or turboprop engines. The ever-rising cost of avgas and doubts about its future availability have spurred a resurgence in aircraft diesel engine production in the early 2010s.

Aircraft maintenance is the performance of tasks required to ensure the continuing airworthiness of an aircraft or aircraft part, including overhaul, inspection, replacement, defect rectification, and the embodiment of modifications, compliance with airworthiness directives and repair.

Blade off testing or blade out testing is a specific form of air safety testing required by the Federal Aviation Administration and other safety agencies to certify safety performance of jet engines. The tests require engine manufacturers to carry out at least two tests of the engine, to make sure that the engine can survive a compressor or fan blade breaking off within the engine and a turbine blade breaking off within the engine, without fragments being thrown through the outside enclosure of the engine, creating an uncontained engine failure.

Aircraft equipped with contra-rotating propellers, also referred to as CRP, coaxial contra-rotating propellers, or high-speed propellers, apply the maximum power of usually a single piston or turboprop engine to drive two coaxial propellers in contra-rotation. Two propellers are arranged one behind the other, and power is transferred from the engine via a planetary gear or spur gear transmission. Contra-rotating propellers are also known as counter-rotating propellers, although counter-rotating propellers is much more widely used when referring to airscrews on separate non-coaxial shafts turning in opposite directions.

Counter-rotating propellers, also referred to as CRP, are propellers which spin in opposite directions to each other. They are used on some twin- and multi-engine propeller-driven aircraft.

A ducted fan is an air moving arrangement whereby a mechanical fan, which is a type of propeller, is mounted within a cylindrical shroud or duct. The duct reduces losses in thrust from the tips of the propeller blades, and varying the cross-section of the duct allows the designer to advantageously affect the velocity and pressure of the airflow according to Bernoulli's principle. Ducted fan propulsion is used in aircraft, airships, hovercraft, and fan packs.

A free-turbine turboshaft is a form of turboshaft or turboprop gas turbine engine where the power is extracted from the exhaust stream of a gas turbine by an independent turbine, downstream of the gas turbine. The power turbine is not mechanically connected to the gas turbine, hence the term "free", referring to the independence of the power output shaft. This is opposed to the power being extracted from the turbine/compressor shaft via a gear box.

The Future Affordable Turbine Engine (FATE) is a US Army program for a 5,000-10,000-shp class turboshaft/turboprop for Future Vertical Lift aircraft and its Joint Multi Role precursor.

A hush kit is an aerodynamic device used to help reduce the noise produced by aircraft jet engines. These devices are typically installed on older turbojet and low-bypass turbofan engines, as they are much louder than later high-bypass turbofan engines.

The hyper engine was a 1930s study project by the United States Army Air Corps (USAAC) to develop a high-performance aircraft engine that would be equal to or better than the aircraft and engines then under development in Europe. The project goal was to produce an engine that was capable of delivering 1 hp/in3 (46 kW/L) of engine displacement for a weight of less than 1 lb/hp delivered. The ultimate design goal was an increased power-to-weight ratio suitable for long-range airliners and bombers.

The Improved Turbine Engine Program (ITEP), formerly the Advanced Affordable Turbine Engine (AATE) program, is a United States Army project to develop a General Electric T700 replacement for the UH-60 Black Hawk and AH-64 Apache, improving fuel consumption, power, durability and cost. Honeywell and Pratt & Whitney formed the ATEC joint venture to develop the T900, while GE Aviation builds the T901. The US Army selected the GE T901 as the winner of the program in February 2019.
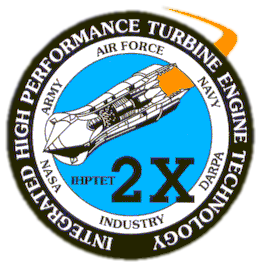
The Integrated High Performance Turbine Engine Technology program was a project of the United States military. Its objective was to conduct science and technology research that would secure advancements in the engineering of the gas turbine engines used in military aircraft. It ran from 1987 until 2005.

Luigi Stipa was an Italian aeronautical, hydraulic, and civil engineer and aircraft designer who invented the "intubed propeller" for aircraft, a concept that some aviation historians view as the predecessor of the turbofan engine.
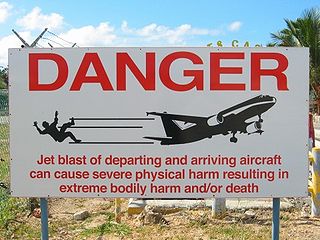
Jet blast is the phenomenon of rapid air movement produced by the jet engines of aircraft, particularly on or before takeoff.

The B-2 was a conversion of Salmson Z9 water-cooled aircraft engines to air cooling by Albert Menasco in the United States.

Paramotor is the generic name for the harness and propulsive portion of a powered paraglider ("PPG"). There are two basic types of paramotors: foot launch and wheel launch.

A podded engine is a jet engine that has been built up and integrated in its nacelle. This may be done in a podding facility as part of an aircraft assembly process. The nacelle contains the engine, engine mounts and parts which are required to run the engine in the aircraft, known as the EBU. The nacelle consists of an inlet, an exhaust nozzle and a cowling which opens for access to the engine accessories and external tubing. The exhaust nozzle may include a thrust reverser. The podded engine is a complete powerplant, or propulsion system, and is usually attached below the wing on large aircraft like commercial airliners or to the rear fuselage on smaller aircraft such as business jets.

A power-egg is a complete "unitized" modular engine installation, consisting of engine and all ancillary equipment, which can be swapped between suitably designed equipment, with standardised quick-changing attachment points and connectors.

Powered paragliding, also known as paramotoring or PPG, is a form of ultralight aviation where the pilot wears a back-mounted motor which provides enough thrust to take off using a paraglider. It can be launched in still air, and on level ground, by the pilot alone — no assistance is required.

A pulse compression detonation system (PCD-system) is a combination of pulse detonation and compression systems.
A pulsejet engine is a type of jet engine in which combustion occurs in pulses. A pulsejet engine can be made with few or no moving parts, and is capable of running statically.

A scramjet is a variant of a ramjet airbreathing jet engine in which combustion takes place in supersonic airflow. As in ramjets, a scramjet relies on high vehicle speed to compress the incoming air forcefully before combustion, but whereas a ramjet decelerates the air to subsonic velocities before combustion using shock cones, a scramjet has no shock cone and slows the airflow using shockwaves produced by its ignition source in place of a shock cone. This allows the scramjet to operate efficiently at extremely high speeds.

A steam aircraft is an aircraft propelled by a steam engine. Steam aircraft were unusual devices because of the difficulty in producing a powerplant with a high enough power-to-weight ratio to be practical. They are distinct from airships that use steam as their lifting gas, which are known as thermal airships.

A supercharger is an air compressor that increases the pressure or density of air supplied to an internal combustion engine. This gives each intake cycle of the engine more oxygen, letting it burn more fuel and do more work, thus increasing the power output.

A turbine engine failure occurs when a turbine engine unexpectedly stops producing power due to a malfunction other than fuel exhaustion. It often applies for aircraft, but other turbine engines can fail, like ground-based turbines used in power plants or combined diesel and gas vessels and vehicles.

A turbocharger, colloquially known as turbo, is a turbine-driven, forced induction device that increases an internal combustion engine's power output by forcing extra compressed air into the combustion chamber. This improvement over a naturally aspirated engine's power output is because the compressor can force more air—and proportionately more fuel—into the combustion chamber than atmospheric pressure alone.

A turboprop engine is a turbine engine that drives an aircraft propeller.

A turboshaft engine is a form of gas turbine that is optimized to produce shaftpower rather than jet thrust. In concept, turboshaft engines are very similar to turbojets, with additional turbine expansion to extract heat energy from the exhaust and convert it into output shaft power. They are even more similar to turboprops, with only minor differences, and a single engine is often sold in both forms.